Best Poster Award (Industry Track) at the European Biomass Conference & Exhibition 2024
Highlights
Lorenzo Aimone and colleagues won the Best Poster Award (Industry Track) at the 32nd European Biomass Conference and Exhibition (EUBCE) for the work titled “Sustainable Biofuels Via Biomass Gasification and Enhanced Waste Heat Recovery Towards Fossil-Free Aluminium Production” by Lorenzo Aimone et al.
The awarded project proposes a novel approach towards the integration of the biomass gasification process directly in an aluminium production site aiming at decarbonizing secondary aluminium industry. This work was developed as part of the NZLV consortium working in close collaboration with Novelis Sierre.
IPESE researcher Lorenzo Aimone receiving the award
Abstract
Currently, the use of woody biomass for industrial energy applications competes directly with its use for domestic heating in Switzerland. Utilizing biomass at low temperatures for household heating not only increases CO2 and particulate emissions but also reduces overall conversion efficiency. Conversely, biomass gasification offers a promising alternative to decarbonize industrial productions, such as secondary aluminium, and to capture and sequester biogenic carbon, aiming for an overall negative carbon balance. This study evaluates the techno-economic feasibility of a biofuels production plant integrated with an aluminium cast house and rolling plant in Switzerland. First, biomass potential and availability are investigated along with the transportation and purchasing costs for the chosen site. Subsequently, the study explores the energy integration between the biomass conversion processes and the aluminium plant. This phase includes modelling a biomass gasifier, various syngas upgrading processes, and furnace technologies (conventional and oxy-fuel combustion of SNG furnaces, and H2 furnaces). A MILP problem is solved to carry out a multi-objective optimization to find economically optimal configurations at different CO2 reduction thresholds at three levels of carbon tax.
Key words: aluminium, decarbonisation, gasification, biomass, synthetic natural gas (SNG), economics
Main Results
A comprehensive literature review on Swiss biomass (wood) potential emphasized the need to enhance its decarbonizing potential by utilizing part of these local bioresources in industrial sectors characterized by hard-to-abate emissions. Secondary aluminium production is a critical industry in which electrification can provide a sustainable alternative only in combustion-based furnaces for medium temperature applications (below 600°C). Methane still represents the optimal fuel to power high temperature furnaces as melters. However, part of the gas exergy is lost in the flue gas leaving the furnaces at temperatures above 1000°C. Using the MILP solver (OSMOSE), a process integration analysis was conducted to explore heat integration between waste heat from the aluminium plant and the biomass conversion process. The biomass conversion benefits from the waste heat generated during aluminium production, meeting its internal heat demand by also partly burning a fraction of the biomass in the reactor. The exothermic nature of biomass gasification and syngas upgrade processes enables heat recovery at lower temperatures, which can be used to co-produce electricity or distributed through a domestic heating network. On the other hand, the aluminium production site can rely on renewable biofuels, such as SNG or hydrogen to run its furnaces. The fuel upgrading process leads to a negative carbon balance because part of the biogenic CO2 is captured to adjust the H2:CO ratio of the syngas. In addition, the use of methane oxy-combustion furnaces facilitates the post-combustion capture. Among the three solutions analyzed (SNG with conventional and oxy-combustion furnaces, and hydrogen with conventional furnaces) using SNG as oxy-fuel results in the highest net negative carbon balance (-240 kg of CO2 per tonne of aluminium) if captured emissions were permanently sequestered. Currently, the site relies entirely on natural gas (NG) from the grid, emitting around 200 kg of CO2 per tonne of product. Powering the entire production site with bioresource would require approximately 1100 kWh of energy from wood per tonne of aluminium. However, the work carried out by the NZLV identified the potential to electrify the rolling plant, which consists of medium temperature furnaces. By prioritizing the use of wood for high temperature furnaces in the cast house, the plant could replace its natural gas consumption (770 kWh) with 560 kWh of biomass per tonne of aluminium.
The multi-objective optimization (Fig. Figure 2) reveals that introducing oxy-combustion furnaces powered by natural gas from the grid can achieve up to a 60% reduction in fossil emissions. However, reaching higher decarbonization targets requires the use of biofuels and capturing their biogenic carbon. Permanent capture of biogenic emissions allows for a mix of fossil natural gas from the grid and SNG to reach net-zero emissions. To achieve this goal, about one-third of the site’s heat demand should be met with wood energy, while the remaining two-thirds should be covered by NG from the grid. Utilizing wood energy provides a biogenic and renewable carbon source, which, if managed correctly, can offset other fossil emissions, maximizing its decarbonizing potential.The economic analysis indicates that, at current energy prices and without a carbon tax, upscaling the process to produce more SNG than necessary for net-zero is not economically viable. However, with an appropriate carbon tax or credit (at least 120€ per tonne of CO2 under current economic conditions), the increased operating costs of expanding the gasification plant capacity could be offset by obtaining carbon credits, thanks to a net negative carbon balance.
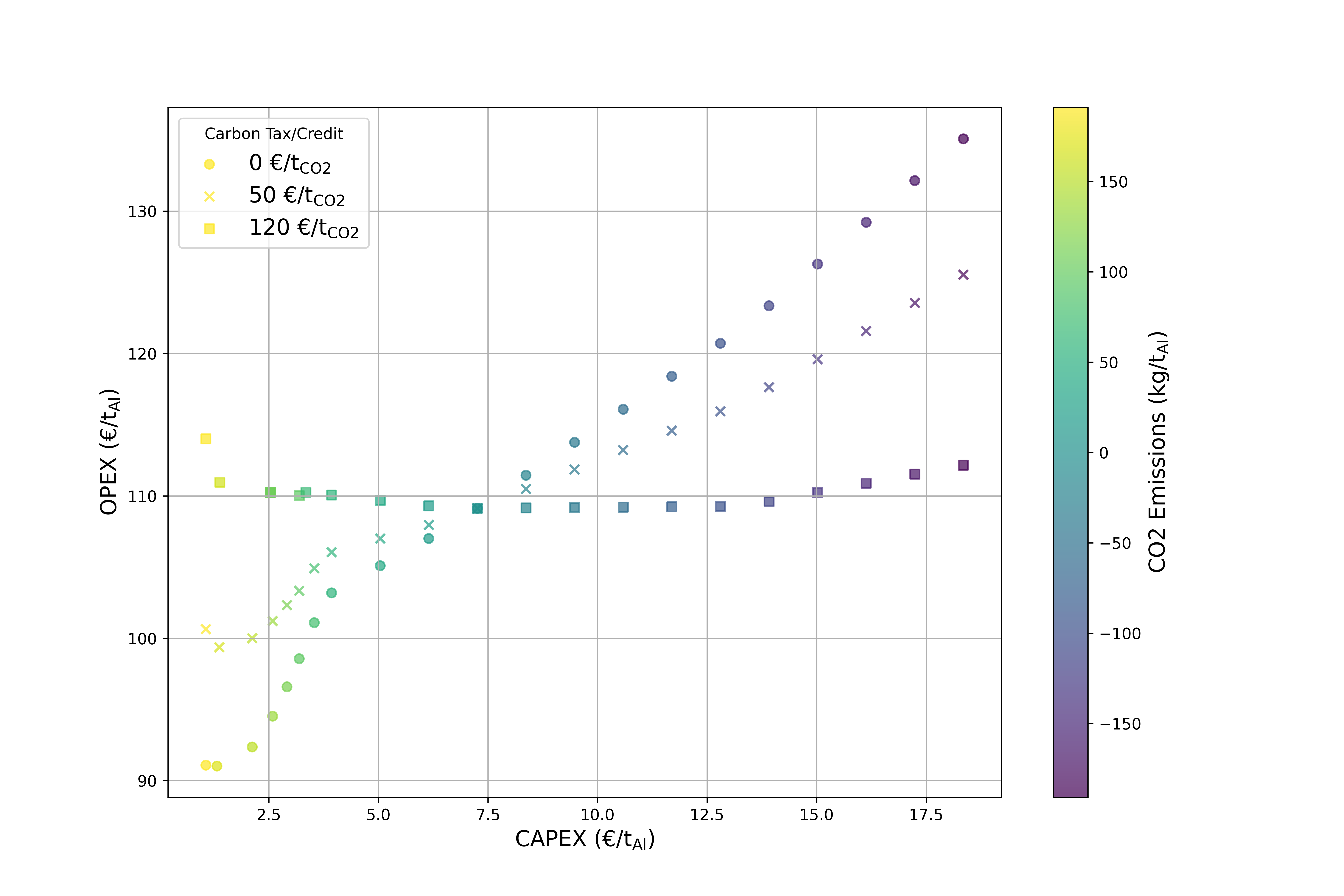
Acknowledgements
The authors thank the Swiss Federal Office of Energy for funding the projects “Sustainable natural gas (SNG) and aluminium production via biomass gasification” and “Enhanced waste heat recovery in Novelis plant in Sierre City” within the Net Zero Lab consortium.
References
[1] Aimone L, Flórez-Orrego D, Dardor D, Germanier R, Maréchal F. “Sustainable Biofuels Via Biomass Gasification and Enhanced Waste Heat Recovery Towards Fossil-Free Aluminium Production”. In: 32nd EUBCE – European Biomass Conference & Exhibition. Marseille, France, 2024.